The goal was to be able to “fly” the 109F/X by the end of the year. I didn’t make it unfortunately. However, things are looking good for a 1st week of 2010!
First up, here’s the completed edge-lit panel for the left sub-panel:
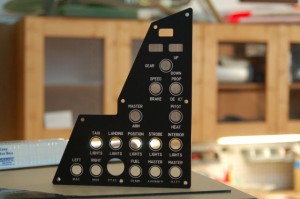
The only problem with the panel is due to a “mid-course” design change that I made. Instead of making the edge-lit panel and metal back plate mounting separate, I decided to combine the two. Since I had done all the panel lettering before I made this change, things on the bottom row kind of got a bit messed up. It’s only really noticeable where the mounting screw passes through the STARTER legend. If I was making this panel for someone else, I would remake it to correct the error.
The wiring on the pitch & roll axis gimbal is now completed. Now that the flight grip has been wired up, it was time to finish out the wiring harness on the gimbal assembly:

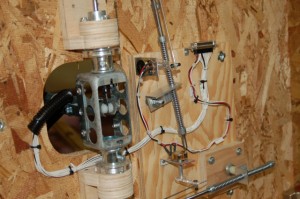
This adds the 16 wires that are needed by the flight grip and the nose wheel/AP disconnect lever. Instead of using tie-wraps to create the new harness, I used waxed lacing cord and then used tie-wraps to attach the harness to nylon cable keeper blocks that have been attached to the gimbal base. The last 6″ or so of the harness up to the DB25 connector is covered with a 1/2″ diameter black plastic split “loom” cover. Makes it look nicer and prevents the wire from being abraded.
I had gotten the SFS box painted the previous evening and now it was time to mount the nose wheel steering/ap disconnect lever to the top of the box:
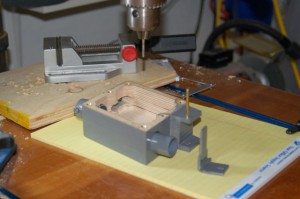
Instead of using a screw & bolt arrangement to hold the NWS/AP lever in, I decided to drill the hole in the side ears just a tiny bit under .125″ and use a brass pin to hold the lever in. In order to properly set the pin, I turned my drill press into an impromptu arbor press by using a 3/32″ drill bit mounted backwards in the drill chuck. I also gave the pin a slight bevel around the ends to make entering the mounting holes easier. Here’s the result:
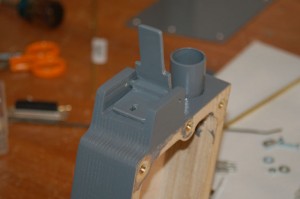
The pin pressed in just as I’d hoped and it won’t work itself out over time. The good part about using the method I did is that the pin can be easily removed in the same manner it was installed if I need to replace or repair the lever in the future.
Now that the lever is in, it was time for the switch:
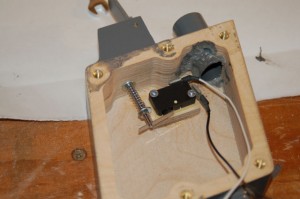
To actuate the micro-switch, I’m using a short length of #4-40 threaded rod as an actuator and a small spring to give it more “pull” than would be provided by the internal spring in the micro-switch. I was able to thread the micro-switch actuating lever with a #4-40 tap. There’s only enough metal for one thread or so, but it works really well! I’m going to put a dab of Loc-Tite on it to help it out.
To retain the actuator rod, I used a brass acorn nut at the top:
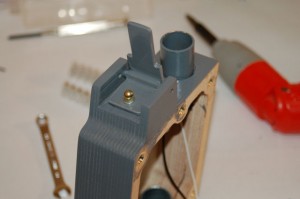
There is a small metal cover that still needs to be made that will cover the front portion of the NWS/AP lever.
The internal wiring of the box took some time to complete and there was not a whole lot of room in there:
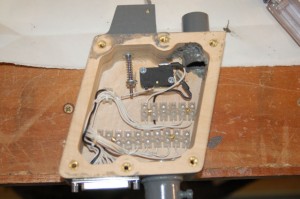
In order to make it more friendly to repair in the future, I decided to use terminal blocks to divide the SFS and grip wiring. Using really small Euro style terminal strips allowed me to pull this off. Even using the small terminal blocks it’s still VERY cramped in there! Like all new wiring I’m doing, this is bound up using waxed lacing tape. I cannot recommend this stuff enough! Had I tried to use small wire-ties in here, it would have been a mess. There just isn’t any room.
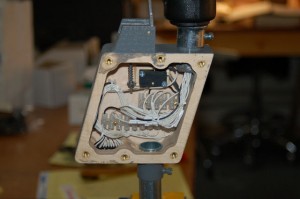
This is what the completed wiring layout looks like. The grip wiring is a bit messier because I didn’t want to shorten any of the wires coming out of the rebuilt Suncom F-15 grip.
Here is what the completed assembly looks like, sans cover:
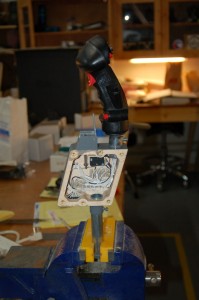
All that’s left is to fab the front cover for the NWS/AP lever and it’ll be totally complete.
Until next time, thanks for reading!